La turbina a gas aeronautica cominciò ad essere sviluppata prima della turbina a gas industriale, nel corso della seconda guerra mondiale, grazie ai consistenti stanziamenti per le spese militari di numerosi paesi coinvolti nel conflitto. Ancor oggi la turbina a gas aeronautica risulta sicuramente più avanzata rispetto agli impianti fissi, anche per effetto di grossi programmi di ricerca sviluppati in ambito militare. Nello specifico settore si sono specializzate alcune aziende che oggi detengono importanti porzioni del mercato (General Electric, Rolls-Royce, ecc.).
I principali requisiti richiesti ad un impianto turbogas per applicazione aeronautica sono:
− potenze elevate e bassi pesi, ovvero elevata potenza specifica;
− ingombri ridotti, particolarmente con riferimento alla sezione trasversale, per ridurre la
resistenza aerodinamica;
− bassi valori del consumo specifico di combustibile (elevato rendimento globale).
Per poter raggiungere elevati valori della potenza e del rendimento è necessario lavorare con alti
livelli della temperatura T3 dei gas caldi all’ingresso della turbina. Ciò si traduce nell’utilizzazione
di materiali pregiati e costosi in grado di resistere ad elevate sollecitazioni ad alta temperatura. Nel contempo vengono utilizzati combustibili pregiati (con basso tenore di zolfo ed ossidi di vanadio) per evitare problemi di corrosione dei materiali operanti ad alta temperatura. Anche la riduzione del peso complessivo dell’impianto viene perseguita attraverso un’attenta scelta dei materiali ed una progettazione ottimizzata del compressore e della turbina, cercando di ridurre al minimo il numero degli stadi di tali turbomacchine.
Per contenere l’ingombro frontale di un motore aeronautico, si cerca di ridurre il diametro massimo di esso, utilizzando compressori e turbine con lo stesso ingombro radiale e realizzando più camere di combustione di dimensione ridotta, operanti in parallelo e disposte tra le due macchine circonferenzialmente all’albero che le collega. In alternativa si realizza un’unica camera di combustione, di tipo anulare, coassiale all’albero.
Al fine di conseguire valori contenuti di consumo specifico generalmente nelle applicazioni
aeronautiche si ottimizza il ciclo di funzionamento in relazione al massimo rendimento, il che
comporta, per assegnati valori della temperatura T3 e dei rendimenti del compressore e della
turbina, la scelta di rapporti di compressione più elevati di quelli che massimizzano il lavoro utile
(vedi figg.6.9 e 6.10). La riduzione del consumo specifico consente, a parità di autonomia del
velivolo, di ridurre la massa di combustibile nei serbatoi e quindi di aumentare il “carico pagante”
dell’aereo.
In un impianto turbogas aeronautico il ciclo termodinamico è evidentemente sempre quello di Joule
I principali requisiti richiesti ad un impianto turbogas per applicazione aeronautica sono:
− potenze elevate e bassi pesi, ovvero elevata potenza specifica;
− ingombri ridotti, particolarmente con riferimento alla sezione trasversale, per ridurre la
resistenza aerodinamica;
− bassi valori del consumo specifico di combustibile (elevato rendimento globale).
Per poter raggiungere elevati valori della potenza e del rendimento è necessario lavorare con alti
livelli della temperatura T3 dei gas caldi all’ingresso della turbina. Ciò si traduce nell’utilizzazione
di materiali pregiati e costosi in grado di resistere ad elevate sollecitazioni ad alta temperatura. Nel contempo vengono utilizzati combustibili pregiati (con basso tenore di zolfo ed ossidi di vanadio) per evitare problemi di corrosione dei materiali operanti ad alta temperatura. Anche la riduzione del peso complessivo dell’impianto viene perseguita attraverso un’attenta scelta dei materiali ed una progettazione ottimizzata del compressore e della turbina, cercando di ridurre al minimo il numero degli stadi di tali turbomacchine.
Per contenere l’ingombro frontale di un motore aeronautico, si cerca di ridurre il diametro massimo di esso, utilizzando compressori e turbine con lo stesso ingombro radiale e realizzando più camere di combustione di dimensione ridotta, operanti in parallelo e disposte tra le due macchine circonferenzialmente all’albero che le collega. In alternativa si realizza un’unica camera di combustione, di tipo anulare, coassiale all’albero.
Al fine di conseguire valori contenuti di consumo specifico generalmente nelle applicazioni
aeronautiche si ottimizza il ciclo di funzionamento in relazione al massimo rendimento, il che
comporta, per assegnati valori della temperatura T3 e dei rendimenti del compressore e della
turbina, la scelta di rapporti di compressione più elevati di quelli che massimizzano il lavoro utile
(vedi figg.6.9 e 6.10). La riduzione del consumo specifico consente, a parità di autonomia del
velivolo, di ridurre la massa di combustibile nei serbatoi e quindi di aumentare il “carico pagante”
dell’aereo.
In un impianto turbogas aeronautico il ciclo termodinamico è evidentemente sempre quello di Joule
(fig.6.11).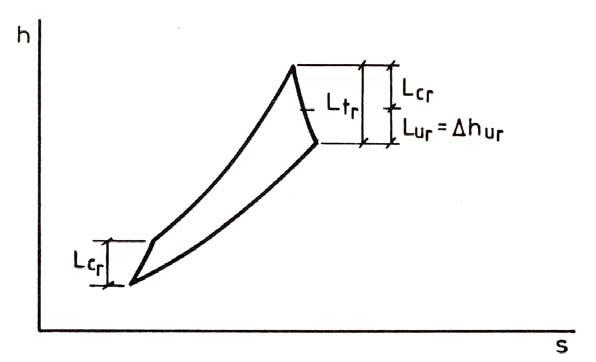
Se il lavoro utile reale Δhur, pari alla differenza tra il lavoro prodotto dalla turbina Ltr e quello
assorbito dal compressore Lcr, viene utilizzato per azionare un’elica, con l’interposizione di un
riduttore di velocità (con rapporto di riduzione in genere compreso tra 10 e 20), si parla di
turboelica. I turboelica sono in genere utilizzati per aerei da trasporto civile o militare e su molti
elicotteri, con potenze da alcune centinaia di kW ad oltre 3.000 kW e con velocità di volo non
elevata (400÷500 km/h). La fig.6.12 illustra lo schema impiantistico di un tipico turboelica.
fig.6.12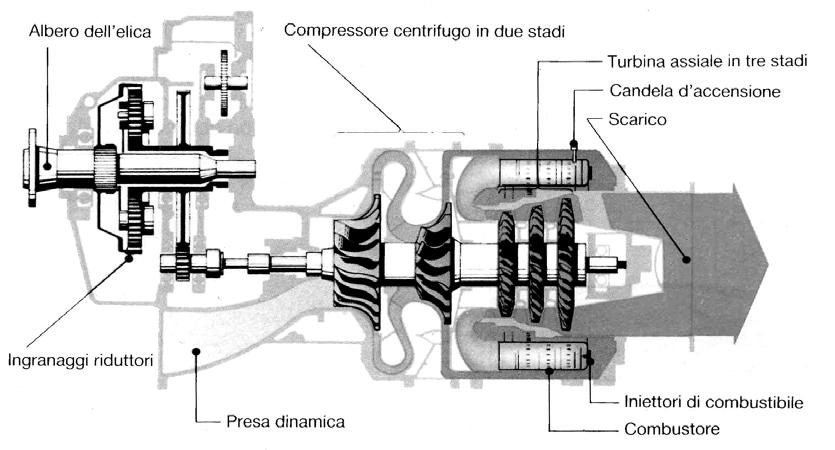
Nella fig.6.13 è invece riportato lo spaccato di un esempio costruttivo di turboelica.
fig.6.13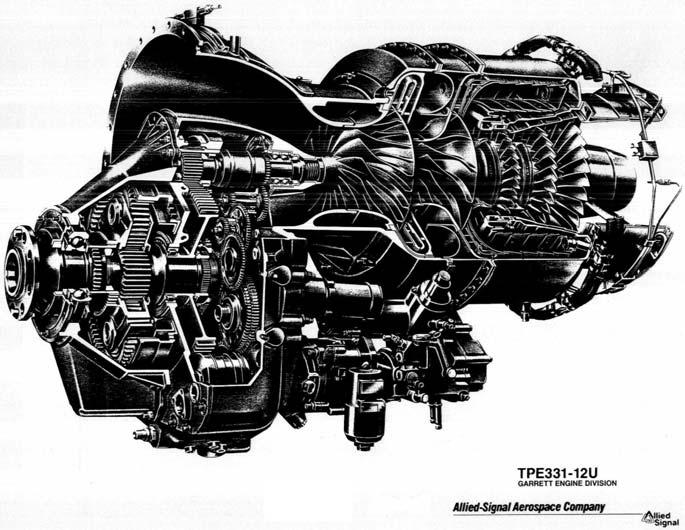
generi solo il lavoro necessario a muovere il compressore. In questo caso il salto entalpico della
turbina è uguale a quello del compressore (fig.6.11) e l’ulteriore salto entalpico disponibile, pari a
Δhur, è convertito in energia cinetica mediante un ugello posto a valle della turbina, dal quale i gas stessi fuoriescono con una velocità vg superiore a quella di volo v dell’aereo. Dalla dinamica è noto che in tal caso nasce per reazione una forza o spinta F uguale e di segno contrario a quella che ha dato luogo all’incremento di velocità del fluido e pertanto pari a:
F = Mg (vg – v)
Dove Mg è la portata di gas che attraversa il turbomotore.
La spinta così generata uguaglia la resistenza aerodinamica totale determinando l’avanzamento
dell’aereo.
In fig.6.14 è riportato lo schema impiantistico di un turbogetto.
fig.6.14
Nei turbogetti vi è anche una presa d’aria, o diffusore, nella quale si realizza una prima
compressione dell’aria per effetto della diminuzione della sua velocità attraverso un condotto
divergente disposto a monte del compressore. Questo processo, detto autocompressione, è
ovviamente molto sensibile ad alte velocità di volo e contribuisce a ridurre il lavoro assorbito dalla
turbomacchina operatrice per l’ulteriore compressione dell’aria.
Il turbogetto è oggi utilizzato per la propulsione in grandi aerei di linea che volano ad alta quota ed
a velocità di 900÷1000 km/h, nonché negli aerei supersonici destinati soprattutto alle applicazioni
militari.
In fig.6.15 è mostrato lo spaccato di un esempio costruttivo di turbogetto. In questo caso, tipico
delle applicazioni civili, si nota una ventola in testa (turbofan) che elabora aria che in parte viene
avviata al compressore ed in parte (aria di by-pass) va ad un secondo ugello che genera anch’esso una spinta. Regolando le due componenti di tale portata d’aria si ottiene una modulazione della spinta con una buona riduzione del consumo di combustibile.
fig.6.15
assorbito dal compressore Lcr, viene utilizzato per azionare un’elica, con l’interposizione di un
riduttore di velocità (con rapporto di riduzione in genere compreso tra 10 e 20), si parla di
turboelica. I turboelica sono in genere utilizzati per aerei da trasporto civile o militare e su molti
elicotteri, con potenze da alcune centinaia di kW ad oltre 3.000 kW e con velocità di volo non
elevata (400÷500 km/h). La fig.6.12 illustra lo schema impiantistico di un tipico turboelica.
fig.6.12
Nella fig.6.13 è invece riportato lo spaccato di un esempio costruttivo di turboelica.
fig.6.13
generi solo il lavoro necessario a muovere il compressore. In questo caso il salto entalpico della
turbina è uguale a quello del compressore (fig.6.11) e l’ulteriore salto entalpico disponibile, pari a
Δhur, è convertito in energia cinetica mediante un ugello posto a valle della turbina, dal quale i gas stessi fuoriescono con una velocità vg superiore a quella di volo v dell’aereo. Dalla dinamica è noto che in tal caso nasce per reazione una forza o spinta F uguale e di segno contrario a quella che ha dato luogo all’incremento di velocità del fluido e pertanto pari a:
F = Mg (vg – v)
Dove Mg è la portata di gas che attraversa il turbomotore.
La spinta così generata uguaglia la resistenza aerodinamica totale determinando l’avanzamento
dell’aereo.
In fig.6.14 è riportato lo schema impiantistico di un turbogetto.
fig.6.14
Nei turbogetti vi è anche una presa d’aria, o diffusore, nella quale si realizza una prima
compressione dell’aria per effetto della diminuzione della sua velocità attraverso un condotto
divergente disposto a monte del compressore. Questo processo, detto autocompressione, è
ovviamente molto sensibile ad alte velocità di volo e contribuisce a ridurre il lavoro assorbito dalla
turbomacchina operatrice per l’ulteriore compressione dell’aria.
Il turbogetto è oggi utilizzato per la propulsione in grandi aerei di linea che volano ad alta quota ed
a velocità di 900÷1000 km/h, nonché negli aerei supersonici destinati soprattutto alle applicazioni
militari.
In fig.6.15 è mostrato lo spaccato di un esempio costruttivo di turbogetto. In questo caso, tipico
delle applicazioni civili, si nota una ventola in testa (turbofan) che elabora aria che in parte viene
avviata al compressore ed in parte (aria di by-pass) va ad un secondo ugello che genera anch’esso una spinta. Regolando le due componenti di tale portata d’aria si ottiene una modulazione della spinta con una buona riduzione del consumo di combustibile.
fig.6.15